Environmental Engineer - Military Veterans
at Veolia Water Technologies & Solutions
ABOUT:
A subsidiary of Veolia group, Veolia North America (VNA) offers a full spectrum of water, waste and energy management services, including water and wastewater treatment, commercial and hazardous waste collection and disposal, energy consulting and resource recovery. VNA helps commercial, industrial, healthcare, higher education and municipality customers throughout North America. Headquartered in Boston, Mass., Veolia North America has more than 10,000 employees working at more than 350 locations across the continent. Please visit our website www.veolianorthamerica.com
BENEFITS
Veolia's comprehensive benefits package includes paid time-off policies, as well as health, dental and vision insurance. In addition, employees are also entitled to participate in an employer sponsored 401(k) plan, to save for retirement. Pay and benefits for employees represented by a union are outlined in their collective bargaining agreement.
POSITION PURPOSE: Responsible for developing and managing the facility environmental programs. Identifies and mitigates environmental risks in support of plant and company performance and reliability goals. Establishes and manages programs directed toward the continuous improvement of environmental objectives. Provides regulatory expertise to strategize and maximize company position within environmental economic programs and interaction with regulatory officials. Coordinates environmental programs with an emphasis placed on identification and communication, and training on regulatory requirements to facility personnel. Provides support to all plant departments and interacts with contractors during expansion projects in an environmental function as well as occasionally project manager functions.
PRIMARY DUTIES / RESPONSIBILITIES
Specific Environmental Compliance Responsibilities include but are not limited to:
The EHS Manager must be knowledgeable in Federal and GA-EPD regulations including CAA, CWA, RCRA, CERCLA, SPCC, SARA, AST, OSHA 1910.120 HAZWOPER, and waste disposal. Responsibilities include:
- Ensuring that plants are compliant with environmental permits and regulations including Title V Air Permit, SPDES Permit, hazardous, universal and solid waste management, and hazardous materials management programs.
- Performing regular environmental audits to monitor compliance of air emissions, water permitted outfalls, and hazardous materials and waste management programs.
- Working with plant staff to develop environmental strategies to prevent incidents and exceedances.
- Maintaining thorough database of environmental related files, records, and sample results.
- Coordinating and managing environmental consultants, contractors, and laboratories The EHS Manager responsibilities include the following media-specific compliance programs. Air Permit Compliance.
- Biomass Fuel compliance.
- CEMS emissions on a daily basis with prediction for month and annual totals.
- CEMS Log review.
- CEMS monitor downtimes.
- Quarterly CEMS reports reviews and submittal.
- Quarterly Excess Emission Reports (EERs).
- Semi-Annual Compliance Report.
- Annual Compliance Report.
- Annual Emissions Inventory Reporting.
- Annual GHG Reporting, if applicable SPDES Permit Compliance Stormwater Water.
- Coordinate required plant sampling.
- Review sampling results prior to submission to GA-EPD.
- Complete any required monthly Discharge Monitoring Reports (DMRs).
- Remain up to date on waste and storm water plant regulations.
- Storm Water Pollution Prevention Plan (SWPPP) Waste Management.
- RCRA Hazardous Waste, classification, accumulation, labeling, manifests, training, recordkeeping.
- Universal Waste program, accumulation, labeling, training.
- Solid waste and recycling accumulation management and disposal for non-hazardous/universal wastes HazMat Management Requirements.
- Oversee implementation of Facility Spill Prevention, Control, and Countermeasures (SPCC) Plan and management of other hazardous chemicals used at the facility.
PHYSICAL REQUIREMENTS / WORK ENVIRONMENT
Must be able to wear protective clothing including protective coveralls, respiratory protection (APR/SCBA). Must be able to work internally in the physical plant and externally on the facility's grounds or at satellite facilities. May be required to work evenings and weekends.
The employee will be required to wear personal protective equipment and clothing where appropriate because of their work around potential hazards such as loud noise, airborne particles, vibration and hazardous materials. This protective equipment includes, but is not limited to, safety eyewear, footwear, hard hat, gloves, hearing protection, and specialized clothing where applicable. Must be able to work in extremes of hot and cold temperatures and inclement weather conditions. Must be able to tolerate dust and other airborne particles and other materials such as diesel and lube oils. Under certain conditions while working in the plant, may be required to wear a respirator - respirators are required in specified areas, therefore the employee will be issued with and trained in the proper use of this equipment. At no time is facial hair permitted. May require repetitive stooping, bending, climbing, reaching, and carrying; intermittent lifting, and moving up to 20 lbs. Must be able to work from ladders, scaffolds, high-lifts, and in confined spaces.
Education / Experience / Background
- Bachelor's Degree in Environmental Science, Engineering, Chemistry, or equivalent.
- Master's degree preferred.
- Minimum of seven years' experience with environmental programs in a power utility or manufacturing industry. Must be familiar with Federal, State of Georgia, and local regulations. Strong interpersonal and written communication skills are required. Requires individuals with a high degree of professionalism. Requires the ability to work well independently and effectively with others, on a daily basis. Successful candidates will also be detail oriented, able to take direction and handle multiple tasks, prioritize work effectively, and see a work project through to completion. A willingness to acquire new skills and utilize technology to streamline processes and problem solve is essential.
Knowledge / Skills / Abilities
- Ability to communicate effectively both orally and in writing.
- Ability to train others in the proper operation of all equipment in the plant.
- Ability to manage multiple projects from start to finish in a timely manner.
- Handle or oversee all procurement for maintenance staff and Major Maintenance projects.
- Develop a floating 5-year LRP for the client and adjust accordingly.
- Be involved in participating in all PSM activities, audits etc.
- Coordinate tracking audits with admin and P.M. as required to maintain updated expenses on all maintenance activities.
- Assist in all safety meetings and safety training at the plant.
- Work alongside Operations Manager to develop a list of maintenance work and planning such activities.
Required Certification / Licenses / Training
- Ability to obtain CSP or CHI certification.
DISCLAIMER:
The salary, compensation and benefits information is accurate as of the date of publication of this notice. The company reserves the right to change this information at any time, subject to applicable law.
We are an equal opportunity employer! All qualified applicants will be considered for employment without regard to race, color, religion, sex, sexual orientation, gender identity, national origin, disability or protected veteran status.
Disclaimer: The salary, other compensation, and benefits information is accurate as of the date of this posting. The Company reserves the right to modify this information at any time, subject to applicable law.
Colbert, GA
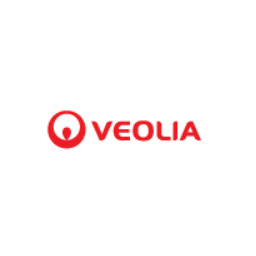
With operations in 130 countries and over 10,000 employees worldwide, Veolia Water Technologies & Solutions (formerly SUEZ – Water Technologies & Solutions) solves the toughest water, wastewater and process challenges around the globe. Leveraging a comprehensive set of chemical, equipment and digital enabled services and products, the company helps customers optimize water resources and overcome process challenges. Veolia Water Technologies & Solutions serves customers across all industries, including food and beverage, metals and mining, power, pharmaceutical, oil and gas, chemicals, petrochemicals, pulp and paper, and utilities.