MAINT SUPERVISOR - OLA, AR - Military Veterans
at PotlatchDeltic
The purpose of this position is to oversee the daily operations of the Maintenance team and their assigned functions. Responsible for the day-to-day maintenance of plant equipment, organizing and monitoring work processes, and coordination of outside contractors. May schedule and supervise fire protection and/or plant services activities to meet the needs of various departments. Ensure that budgeted Key Performance Indicators (KPI’s) are achieved with a focus on safety, up-time, efficiency, and housekeeping. Train and supervise maintenance team members. Support and ensure a positive culture at the Ola facility is a safe, clean, efficient, and desired location for team members to work. Perform other duties as assigned.
The salary range for this position is $73,800-$123,000.
This position is bonus eligible, with a target value of 10% salary.
Key Activities:
Leadership:
Provide leadership in the development of hourly team members through training, daily coaching, and performance review feedback on all equipment and processes in area of responsibility. Encourage team member involvement, information sharing, problem solving, total quality and process improvement teams.
Continuous observation of millwrights to ensure that job descriptions are adequate and current. This will ensure improved training and overall recruitment.
Continuous observation of millwrights to verify skillsets to properly monitor progression through the Pay for Skills Trades program.
Provide information and training for team members on all equipment and processes in areas of responsibility.
Complete all hourly payroll approvals. Time approvals must be approved by the end of the production week and no later than Monday morning of the week following 7:00 a.m.
Overtime continuously monitored with the goal of achieving 13% or less.
Approval of team members paid time off (PTO) and turn in necessary paperwork to HR for processing timely.
Participate in interviews and selection process of team members as well as the selection process through the job bidding policy.
Provide HR timely documentation regarding occurrence reports, progressive disciplinary actions on attendance of team members, performance reviews, performance related disciplinary actions, training opportunities, and other paperwork as deemed necessary.
Provide an atmosphere that leads to continual improvement in safety, quality, and productivity.
Create a positive culture environment where team members are noticed/acknowledged daily, their ideas and suggestions are heard, they are treated with respect and kindness, and they are greeted with empathy and concern for their overall well-being.
Maintenance & Reliability:
Maintain professional and technical knowledge/expertise.
Ensure that Work Orders for failures are created and accurately describe in detail the corrective actions needed.
Verify parts for Work Orders are checked out properly.
Ensure that all completed work was done safely, timely, efficiently and that you or a lead has properly signed the work order verifying that work was performed satisfactorily.
Set schedules, goals, objectives, and support the other teams of the operation process.
Assist operations to achieve and maintain budgeted production levels with a focus on safety, up-time, and efficiency.
Identify and correct any potential problems (troubleshooting) and take appropriate action necessary to prevent serious equipment failure. Monitor Predictive and Preventative Maintenance (PM) activities and follow up to maximize machine efficiency and availability.
Plan effective use of available resources and assist in the development of process, design, and operational improvements.
Identify projects for new technology or processes to improve recovery, uptime, and productivity.
Identify possible cost savings in the mill while being mindful of overall cost and impact to production output.
Coordinate activities of outside contractors in compliance with the site’s contractor program.
Supervise and schedule fire protection for all hot work jobs.
Safety & Environmental:
Maintain a safe, clean, environmentally compliant facility and a work atmosphere conducive to promoting and encouraging safe working behaviours. Encourage team member accountability with an understanding of consequences to performing unsafe acts.
Lead, participate in, and promote all safety activities including regular safety meetings, attending the plant wide safety team meetings, and promoting near miss/hazard recognition reporting.
Continuous compliance with all team members regarding SLAM card policy with each task being challenged and verified.
Continuous compliance with all team members regarding LOTOTO policy with each task being challenged and verified with proper lock out and testing.
Ensure adequate security and protection from hazards (fire etc.)
Continuous compliance with all team members regarding Hot Work Permit policy with each task being challenged and verified.
Ensure that team members are following all protocols of the Firewatch program.
Ensure that all safety/environmental recordkeeping is completed in a timely manner by reporting and completing necessary paperwork timely.
Safety observations and near miss forms completed weekly and turned in to Safety coordinator for tracking of leading indicators.
Ensure that all team members are given the opportunity to complete monthly Vivid Trainings with a goal of 100% monthly compliance. Variance in compliance needs to be documented.
Allow safety committee team members to be active and participate in activities and meetings as required.
Operate the assigned areas in compliance with environmental regulations and other state/federal laws/regulations to ensure compliance.
Provide information and training on OSHA rules and regulations and additional site procedures. Conduct daily, weekly, and monthly safety training and document as required.
Monthly walk around housekeeping audits including pictures and descriptions with a corrective plan of action, communicated with teams via email, to address concerns and ensure that all team members have a focus of continuous improvement in safety and housekeeping compliance.
Requirements:
High school diploma or GED required. Bachelor’s degree in manufacturing, engineering or related preferred.
Minimum of three-five years of related industry maintenance experience. One year of leadership/supervisory experience and/or on a major project.
Knowledge of Excel, Word, and UltiPro systems preferred. Intermediate proficiency in a maintenance management system (AX or Maximo system preferred).
Excellent written and verbal communication skills required.
Must have good organizational and computer skills.
Must be self-motivated and energetic.
Resume and references requested upon completion of application.
We offer a comprehensive benefit package that includes medical, dental, vision, 401(k), life and disability insurance, paid time off and additional voluntary benefits.
PotlatchDeltic is an EEO/AA/M/F/Veteran/Disabled Employer.
Ola, AR
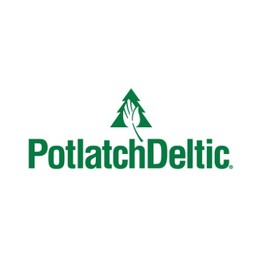
PotlatchDeltic is a Real Estate Investment Trust (REIT) that owns nearly 1.9 million acres of timberland in Alabama, Arkansas, Idaho, Louisiana, Minnesota and Mississippi. Through its taxable REIT subsidiary, the company also operates six sawmills, an industrial-grade plywood mill, a residential and commercial real estate development business and a rural timberland sales program. PotlatchDeltic, a leader in sustainable forest practices, is dedicated to long-term stewardship and sustainable management of its timber resources.