Lean Services Manager, Advanced Facilities Group - Military Veterans
at J.E. Dunn Construction Group, Inc.
Best People + Right Culture. These are the driving forces behind JE Dunn’s success.
By hiring inspired people, giving them interesting and challenging work, enabling them with innovative tools, and letting them share in the company’s rewards, we’ve found a sustainable way to grow in our industry for the last 100+ years.
Our diverse teams around the country strive to enrich lives through inspired people and places everyday, and we need inspired people like you to join us in our pursuit of building perfection.
JE Dunn’s Advanced Facilities Group (AFG) combines Mission Critical, Advanced Industries, and Industrial & Manufacturing into one high-performing team focused on cutting-edge work to serve innovative clients on large Industrial & Manufacturing, Data Center, and Semiconductor projects. As part of the Advanced Facilities team, you'll work on some of the most advanced construction projects across the country, growing your career alongside our diverse team of industry professionals.
Role Summary
The Lean Services Manager will provide leadership and oversight to our Process Improvement and Knowledge Management initiatives and/or manage Lean processes and resources at a regional level. This position will be responsible for co-developing the national Lean strategy, establishing Lean practices and ensuring Lean training and coaching delivery. All activities will be performed in support of the strategy, vision and values of JE Dunn.
Key Role Responsibilities - Core
LEAN SPECIALIST FAMILY - CORE
- Trains internal staff on Lean tools. Helps develop and maintain Lean transformation processes and programs.
- Coaches and supports project teams and/or internal customers with implementation of the basic Lean tools such as Last Planner System, Kanban, meeting facilitation and continuous improvement programs.
- May lead and train PMs and Superintendents to run effective Pull Planning sessions, weekly Planning sessions and Daily Stand-up sessions through a lead/co-facilitate/coach model.
- Actively participates in the development and maintenance of the organization’s ongoing Lean journey.
- Challenges project team members and employees to identify, remove and resolve constraints that prevent the team from fulfilling commitments.
- Maintains level of standards of lean tools used among project teams or within the organization.
- Trains and supports the office and/or region with basic lean tools including but not limited to, Value Stream Mapping, A3’s, 5S, Visual Management, Kanban and Kaizen.
- Trains and coaches employees and team members to understand the Work Flow Commitment Loop (reliable promising).
- Assumes responsibility for bringing all components of the Last Planner System together to function as a system. Trains and coaches the team in LPS practices.
- Utilizes current training materials and customizes to specific assigned customer.
- Looks for opportunities to improve current training materials.
- Serves as an ongoing resource for assigned projects and employees to help identify opportunities for improvement.
Key Role Responsibilities - Additional Core
LEAN SERVICES MANAGER
In addition, this position will be responsible for the following (LSM):
- Works with and supports National departments to bring Lean into all aspects of work.
- Trains and coaches on process improvement, A3s and other Lean tools.
- Coaches those in leadership on Lean.
- Assumes responsibility for training and development plans for Lean Specialists.
- Serves as a thought partner with National Director of Lean for overall Lean Strategy Deployment.
- Develops marketing messages that support a national Lean strategy.
- Manages Lean Specialists.
- Trains and coaches employees and team members to understand the Work Flow Commitment Loop (reliable promising).
- Trains internal staff on Lean tools and helps develop and maintain Lean transformation processes and programs.
- Actively participates in the development and maintenance of the organization’s ongoing Lean journey.
- Responsible for owning the training materials including developing, improving, maintaining and finding new materials.
Knowledge, Skills & Abilities
- Ability to perform work accurately and completely, and in a timely manner.
- Communication skills, verbal and written (Advanced).
- Proficiency in MS Office (Intermediate).
- Ability to facilitate meetings and build consensus.
- Ability to conduct effective presentations (Intermediate).
- Ability to provide performance management feedback and complete evaluations.
- Ability to manage a team.
- Ability to coach (Intermediate).
- Ability to adapt and respond to dynamic situations (Intermediate).
- Ability and desire to master new skills (Intermediate).
- Ability to lead change management and Lean efforts (Intermediate).
- Listening skills (Intermediate).
- Ability to read a situation and make sound recommendations (Intermediate).
- Ability to speak confidently in large sized groups.
- Open learner and highly coachable.
- Knowledge of Lean process and philosophy (Intermediate).
- Ability to build relationships and collaborate within a team, internally and externally.
Education
- Bachelor’s degree in construction management, business management or related field (Preferred).
- In lieu of the above requirements, equivalent relevant experience will be considered.
Experience
- 5+ years of Lean management or consulting experience (Required).
- 5+ Years people management experience (Required).
- 2+ Years financial management experience (Required).
- 2+ Years experience in meeting or group facilitation (Required).
- 2+ years experience implementing process improvement methodologies or other Lean tools and techniques (Required).
- 5+ years construction operations experience (Preferred).
Working Environment
Benefits Information
The benefits package aligned to this position is Professional Non-Union. Please click the link below for more details.
Click here for benefits details.
JE Dunn Construction is committed to hiring and retaining a diverse workforce. We are proud to be an Equal Opportunity/Affirmative Action Employer and it is our policy to provide equal opportunity to all people without regard to race, color, religion, national origin, ancestry, marital status, veteran status, age, disability, pregnancy, genetic information, citizenship status, sex, sexual orientation, gender identity or any other legally protected category. JE Dunn Construction is a background screening, drug-free workplace.
JE Dunn provides reasonable accommodations to qualified individuals with disabilities. If you would like to request a reasonable accommodation in order to apply for a job, please submit your request to accommodations@jedunn.com
JE Dunn Construction Company does not accept unsolicited resumes from search firms or agencies. Any resume submitted to any employee of JE Dunn Construction without a prior written search agreement will be considered unsolicited and the property of JE Dunn Construction Company. Please, no phone calls or emails. #INDAFG
Atlanta, GA
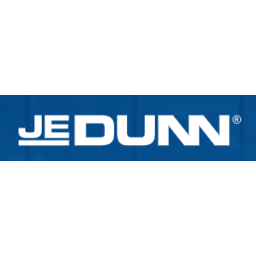
JE Dunn Construction Company is family and employee owned and has been a leader in the commercial construction industry since 1924. Headquartered in Kansas City, Missouri, JE Dunn has 24 offices nationally and employs over 3,500 employees. The company provides general contracting, construction management, and design-build services. According to Engineering News-Record (ENR) magazine, JE Dunn is ranked consistently among the top contractors nationwide. JE Dunn is an industry leader in the application of preconstruction technology, virtual design and construction, and other emerging construction technologies. Innovation in construction, client-centric problem-solving, and delivering an exceptional client experience is what differentiates us in the industry.